Our technical services program is meticulously managed and overseen by a team of highly experienced professionals, including Master Mariners and Chief Engineers. Their expertise ensures the highest quality outcomes while maintaining cost and time efficiency. Upon receiving a service inquiry, our team conducts a thorough evaluation of the customer’s expectations and requirements. This assessment forms the basis of a comprehensive and effective repair & service plan, offering competitive and reasonable rates tailored to the specific needs of our clients.
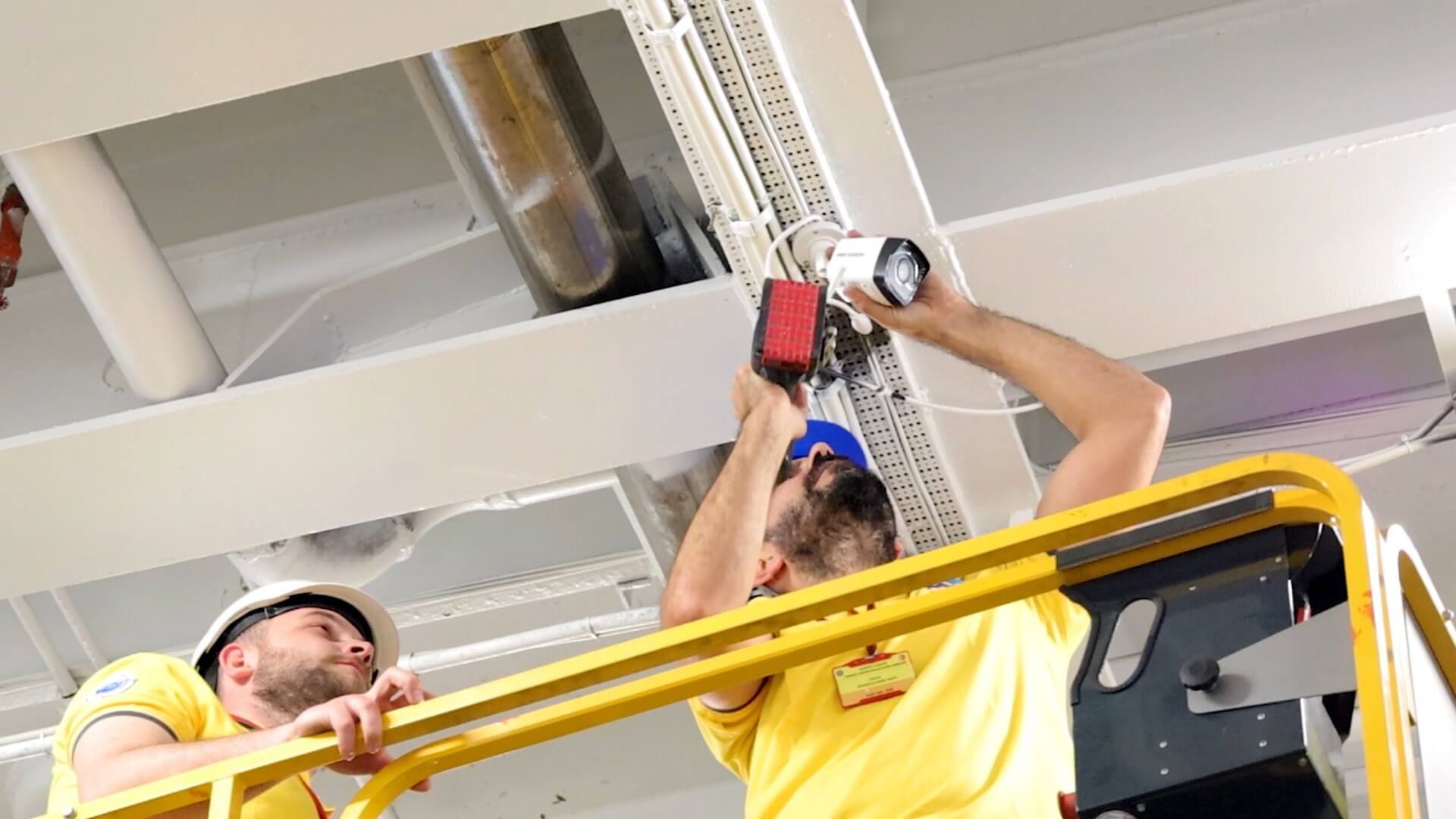
Initial Assessment and Planning
To ensure the best possible results, we employ a dual approach. Firstly, we utilize our skilled boarding team, adept at handling a wide range of technical services directly on the vessel. This team has extensive maritime knowledge and experience, enabling them to address and resolve issues effectively. Secondly, we collaborate with our network of approved third-party workshops and technicians. These partnerships allow us to extend our capabilities and resources, ensuring that all necessary repairs and maintenance are conducted to the highest standards.
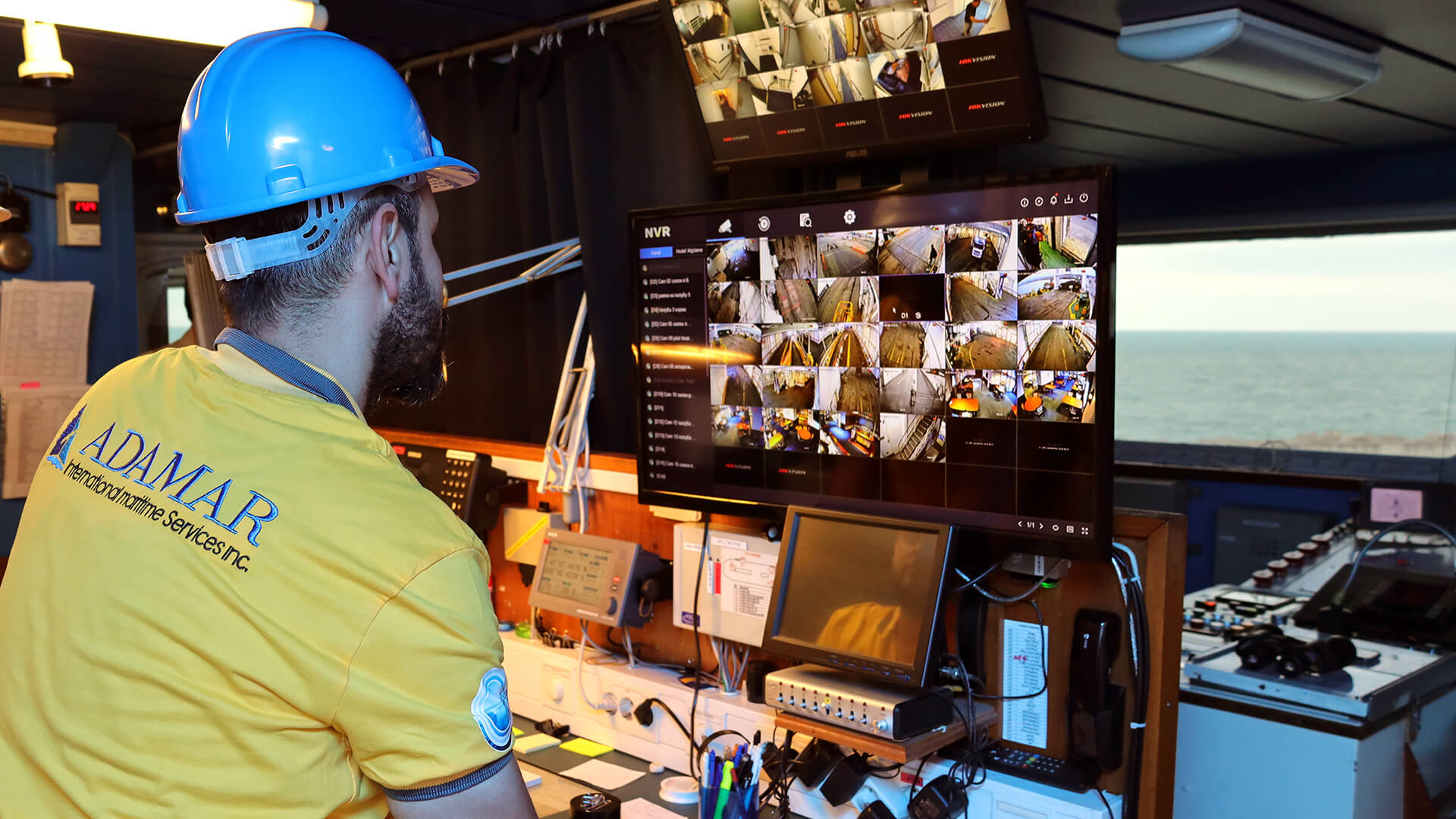
Riding Team for Continuous Operation
For customers who require their vessel to remain operational and avoid being off-hired during the repair process, we offer the services of our riding team. This team, comprised of qualified professionals holding Seaman’s Books and Schengen visas, is uniquely equipped to travel and work onboard vessels seamlessly. The riding team can perform essential repairs and maintenance while the vessel continues her operations, offering a flexible solution that minimizes downtime and maximizes operational efficiency for our clients, ensuring a smooth and uninterrupted operation.
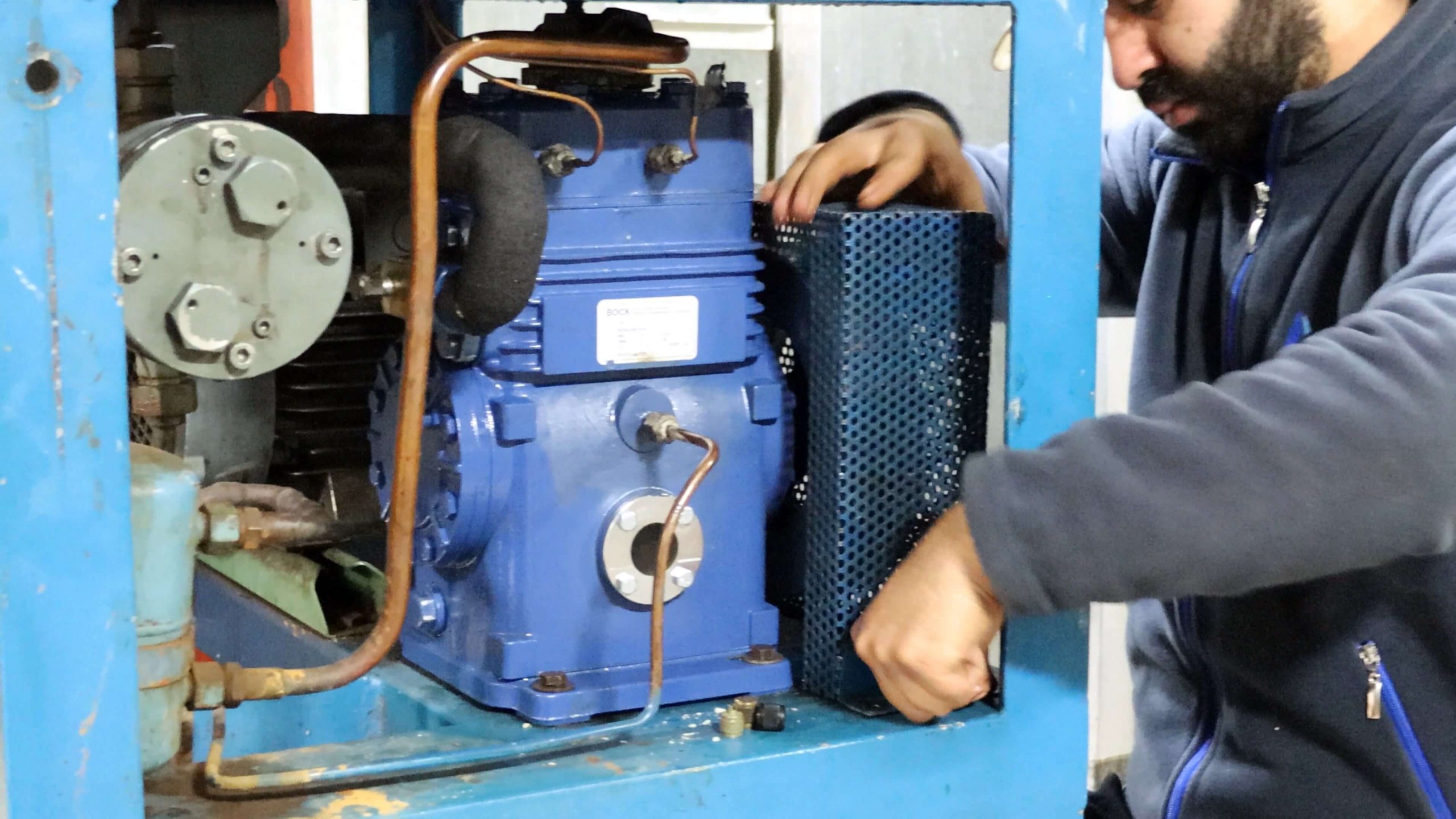
Commitment to Quality and Efficiency
Our commitment to quality and efficiency is not just a statement; it's a reflection of our values. It's demonstrated in every aspect of our technical services program. By strategically utilizing the expertise of our marine background staff and our network of trusted third-party resources, we ensure that our clients receive top-tier services that meet their specific needs and expectations. Whether through direct intervention by our boarding team or through coordinated efforts with our partners, we are dedicated to delivering effective and economical solutions, providing our clients with the best value for their investment.
Committed for Superior Solutions
Briefly, our technical services program is designed to provide unparalleled support to our clients, combining the knowledge and skills of experienced maritime professionals with a robust network of third-party collaborators. This integrated approach allows us to deliver high-quality, cost-effective solutions tailored
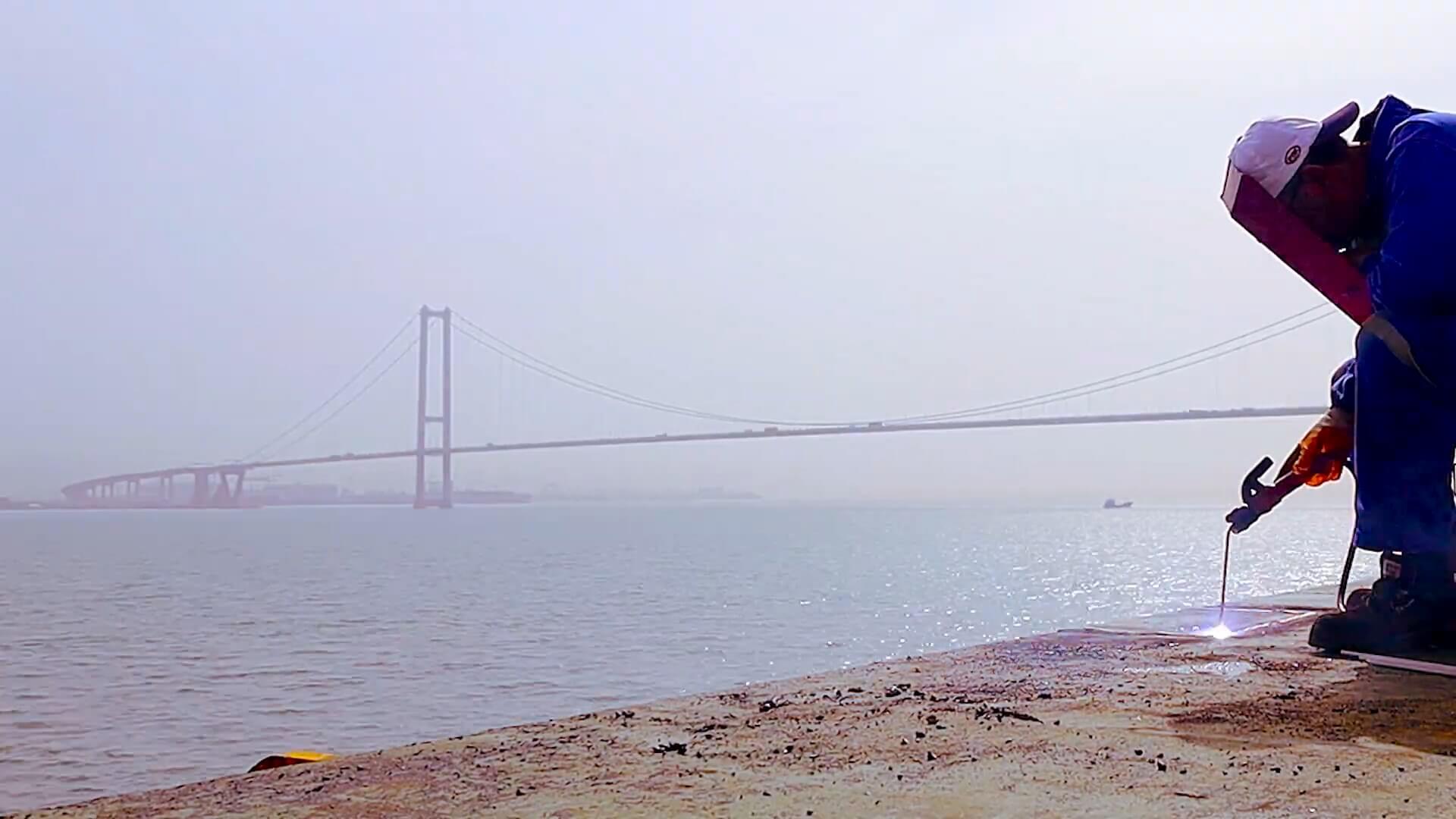
What services do we offer?
The list of services provided is as follows:
- M/E and A/E Repairs and Overhauls
- Annual & 5-Yearly Inspections of FFE & LSA (SCBA, EEBD, Fixed FFE, Portable FFE, etc.)
- Annual & 5-Yearly Inspections of Liferafts, Lifeboats & Davit Inspections
- GMDSS & Bridge Equipment Inspections, Rado Surveys, Services, and Spare Parts Supply
- Calibration & Certification of Various Types of Equipment (ODME, 15 PPM, Other Various Sensors & Gauges)
- Class Approved Underwater Hull Inspections & Temporary Overboard Pluggings
- UTM (1st, 2nd, 3rd SS with IACS Class Approved Companies), Ultrasound Test and NDT
- Seachest and Propeller Cleaning, Anode Installation
- Fabrication, Repair & Installation of Class Approved Accommodation & Plot Assist Ladders
- Fabrication of Ship Specific Structures and Fittings (Manholes, Access Hatches, Ventilation Openings, Windlass Parts, Ship Specific Piping & Fittings)
- Anchor & Anchor Chan Cable Replacement
- Cargo Hold Cleaning & Coating Services
- Accommodation A/C Repair Service
- Cargo Hatch Cover Ram Overhaul & Rod Replating
- Incinerator & Boler Repair and Services
- Governor Overhaul and Exchange
- PLC & PCB Card Repair and IT Services
- Certified Steel Plate Renewal and WPQR/WPS Certified Welding Jobs
- Tank Radar and Cargo Monitoring System Repair
- Propeller Boss Cap Fins Instillation (PBCF)
FAQ
Frequently Asked Questions
Frequently Asked Questions About Services & Repairs
Adamar provides technical services for various vessels, including general cargo vessels, tankers, container ships, bulk carriers, and offshore vessels. Our experienced team can handle the specific needs of various maritime vessels.
Don’t hesitate to get in touch with us through e-mail at services@adamarine.com and sales@adamarine.com, as well as via phone or direct messaging with one of our team members. Provide us with the details of your requirements, and our team will respond promptly with a tailored plan and a competitive quote.
Our technical service team is comprised of highly experienced professionals, including Master Mariners and Chief Engineers, who possess extensive maritime backgrounds. Their expertise ensures that we deliver superior quality services with a strong focus on cost and time efficiency.
Quality and safety are our top priorities. We adhere to flag and class standards and regulations, use certified technicians and workshops, and conduct thorough inspections and tests. Our team’s extensive experience and commitment to excellence ensure that all services are performed to the highest standards.
Upon receiving a service inquiry, our team thoroughly evaluates the customer’s expectations and requirements. Then, we develop a tailored plan that offers reasonable and competitive rates. Our goal is to provide high-quality services at the best possible price and offering a lumpsum quote as much as possible.
Yes, to ensure the best results, we collaborate with approved third-party workshops and technicians when necessary. This allows us to leverage additional expertise and resources, ensuring comprehensive and effective service delivery.
Yes, we offer emergency repair services to address urgent issues that may arise on your vessel. Our team is equipped to respond quickly and effectively to minimize downtime and ensure the safety and operational efficiency of your vessel.
Yes, we can provide certain services while the vessel is in operation. Our riding team, equipped with Seaman’s Books and Schengen visas, can board the vessel and perform necessary repairs and maintenance without disrupting its schedule and causing off-hire.
For complex repairs and overhauls, we utilize a combination of our highly skilled in-house team and trusted third-party workshops. Under the supervision of a service engineer on board, we conduct detailed assessments and planning to ensure all aspects of the repair or overhaul are meticulously addressed.
Our key priority is ensuring minimal downtime during our services by prioritizing efficiency and meticulous planning. By coordinating closely with TSI and all parties, we aim to complete services quickly and effectively, minimizing any disruption to your vessel’s schedule.
We keep our customers informed through regular updates and communication. You can stay updated on the status of ongoing services via email, phone calls, or direct messages, ensuring transparency and peace of mind throughout the service process.
Yes, we perform certified steel plate renewals and Welding Procedure Qualification Records (WPQR)/Welding Procedure Specifications (WPS) certified welding jobs, ensuring high-quality and compliant work.
We maintain a robust supply chain for spare parts and equipment, ensuring availability and timely delivery. Our partnerships with reputable suppliers and manufacturers allow us to source genuine or OEM parts as per lead time and client’s request.
We offer our services globally, with the capability to deploy teams and equipment to various locations thanks to our trusted partners around the world. Our extensive network of approved third-party workshops and technicians allows us to provide comprehensive support wherever your vessel is trading.
We can fabricate in our own workshop and install on board a wide range of ship-specific structures and fittings, including manholes, access hatches, ventilation openings, windlass parts, and piping. All fabrications are tailored to the unique needs of each vessel and meet class standards.
We install Propeller Boss Cap Fins (PBCF) to enhance the efficiency and performance of propellers, contributing to fuel savings and reduced emissions.
Choosing our technical services program offers several benefits, including access to highly qualified marine professionals, competitive pricing, and a comprehensive range of services. Our focus on quality, safety, and efficiency ensures that your vessel receives the best possible care under Adamar’s assurance.
Services
Contact Us
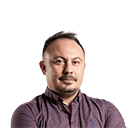
Executive Director
Baris PEZUK
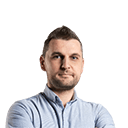
Executive Director
Soner CIHAN
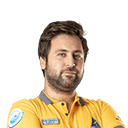
Service & Repair Division Manager
Eray SABANCI
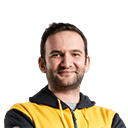
Service & Repair Division Executive
Kubilay YUCE
Request a Quote
Please fill in the form below so we can send you our best offer right away!